Continuous improvement lies at the heart of every successful organization's Quality Management System (QMS).
In today's rapidly evolving business landscape, where customer expectations and regulatory requirements are constantly changing, adapting and improving business processes is essential for sustained success.
The ‘why’ behind continuous improvement processes within a QMS involves ongoing efforts to enhance processes, products, or services. It is a structured approach that fosters a culture of learning, innovation, and adaptation within an organization.
Keep reading to learn popular models, benefits, challenges, and real stories of continuous improvement in QMS.
What is Continuous Improvement for QMS?
Continuous improvement is a foundational principle of Quality Management Systems (QMS), embodying the relentless pursuit of small improvements to enhance processes, products, and services. Originating from Japanese manufacturing philosophies, notably Toyota's lean production system, continuous improvement focuses on incremental changes that collectively yield significant enhancements over time. This approach contrasts with the American inclination towards dramatic, one-time innovations, emphasizing instead the value of steady progress through continuous process improvement.
Key methodologies within continuous improvement include the use of Kanban boards, which facilitate visual process management and help teams identify and address bottlenecks efficiently. Teamwork is crucial, as team members collaboratively assess current processes, implement new processes, and reduce cycle times. By focusing on incremental changes, organizations can achieve sustainable growth and adaptability, ensuring that each small improvement contributes to a more efficient and effective QMS.
Common Continuous Improvement Models
Continuous improvement in QMS can be facilitated through various structured models and methodologies. Each model offers unique approaches to identifying, analyzing, and implementing improvements within an organization.
Here are some prominent improvement techniques:
Plan-Do-Check-Act (PDCA)
The PDCA cycle, also known as the Deming Cycle, is a fundamental continuous improvement model widely adopted across industries. This four-step method includes the following stages:
- Plan: Identify opportunities for improvement and develop a plan.
- Do: Implement the plan on a small scale.
- Check: Evaluate the results and collect data on metrics.
- Act: Take action based on the results to standardize or improve further.
This model emphasizes learning from each cycle to refine processes continuously.
Six Sigma
Six Sigma focuses on reducing defects and variation in processes to improve quality and efficiency. It utilizes a structured approach known as DMAIC:
- Define: Clarify the problem and project goals.
- Measure: Quantify current performance and collect data.
- Analyze: Identify root causes of issues.
- Improve: Implement solutions to address identified problems.
- Control: Maintain improvements and monitor performance.
By following DMAIC, organizations can achieve significant improvements in process capability and customer satisfaction.
Kaizen
Kaizen, originating from Japan, translates to "change for the better" and embodies a philosophy of continuous, incremental improvement. Unlike other models, Kaizen emphasizes making small changes over time rather than large-scale transformations. Key principles include:
- Standardization: Establishing standardized processes.
- Elimination of Waste: Identifying and eliminating unnecessary steps or activities.
- Employee Involvement: Engaging employees at all levels to contribute ideas for improvement.
Kaizen fosters a culture of continuous improvement and is particularly effective in cultivating innovation and efficiency.
Total Quality Management (TQM)
TQM is a comprehensive approach to project management that focuses on improving quality across all organizational processes. It integrates principles of quality management into the organization's culture and involves:
- Customer Focus: Understanding and meeting customer needs and expectations.
- Employee Involvement: Engaging employees in quality initiatives and decision-making.
- Process Approach: Managing activities and resources as interconnected processes.
- TQM aims to enhance customer satisfaction and achieve long-term success through continuous improvement efforts.
Lean Manufacturing
Lean principles aim to maximize value while minimizing waste in manufacturing processes. It focuses on identifying and eliminating non-value-added activities, known as "muda," through techniques such as:
- Value Stream Mapping: Analyzing and visualizing the flow of materials and information.
- Just-in-Time (JIT): Delivering products or services only when needed, reducing inventory and waste.
- Continuous Flow: Ensuring smooth, uninterrupted flow of work through processes.
Lean methodologies optimize efficiency and improve responsiveness to customer demands.
Choosing the Right Model
The selection of a continuous improvement model depends on organizational goals, industry-specific requirements, and the current state of processes. Many organizations adopt hybrid approaches, combining elements of different models to suit their unique needs. Regardless of the model chosen, the key to successful implementation lies in leadership commitment, employee engagement, and a systematic approach to identifying and implementing improvements.
Implementing Continuous Quality Improvement
Implementing continuous improvement begins with establishing a robust framework that aligns with organizational goals and values. Here are the key steps:
- Leadership Commitment: Leadership plays a crucial role in driving continuous improvement. When leaders prioritize and actively participate in improvement initiatives, they set a precedent for the entire organization.
- Employee Involvement: Engaging employees at all levels is vital. Front-line staff often have valuable insights into daily operations and customer interactions, making their involvement essential for identifying improvement opportunities.
- Training and Development: Providing training on continuous improvement methodologies equips employees with the skills needed to contribute effectively. Continuous learning ensures that the organization remains adaptive and responsive to change.
Benefits of Continuous Improvement in QMS
- Enhanced Efficiency: Streamlining processes through continuous improvement reduces unnecessary steps and optimizes resource allocation, leading to increased productivity.
- Improved Quality: By identifying and addressing the root causes of issues, organizations can consistently deliver products and services that meet or exceed customer expectations.
- Cost Reduction: Eliminating waste and inefficiencies directly translates into cost savings. Whether through reduced rework or improved resource utilization, financial benefits are tangible.
- Competitive Advantage: Organizations that continuously improve their QMS are better equipped to adapt to market changes and outperform competitors.
Challenges and Considerations
While the benefits of continuous improvement are clear, implementing and maintaining an effective QMS requires overcoming several challenges including:
- Resistance to Change: Some employees may be resistant to new methodologies or processes, necessitating effective change management strategies.
- Resource Constraints: Allocating sufficient time, budget, and personnel to improvement initiatives can be challenging, especially for smaller organizations.
- Sustainability: Ensuring that improvements are sustained over time requires ongoing monitoring and reinforcement.
Case Studies in Continuous Improvement
There are many impressive continuous improvement examples, and Propel customers have seen major success by leveraging our QMS to:
Unify Existing Systems – From 6 Systems to 1
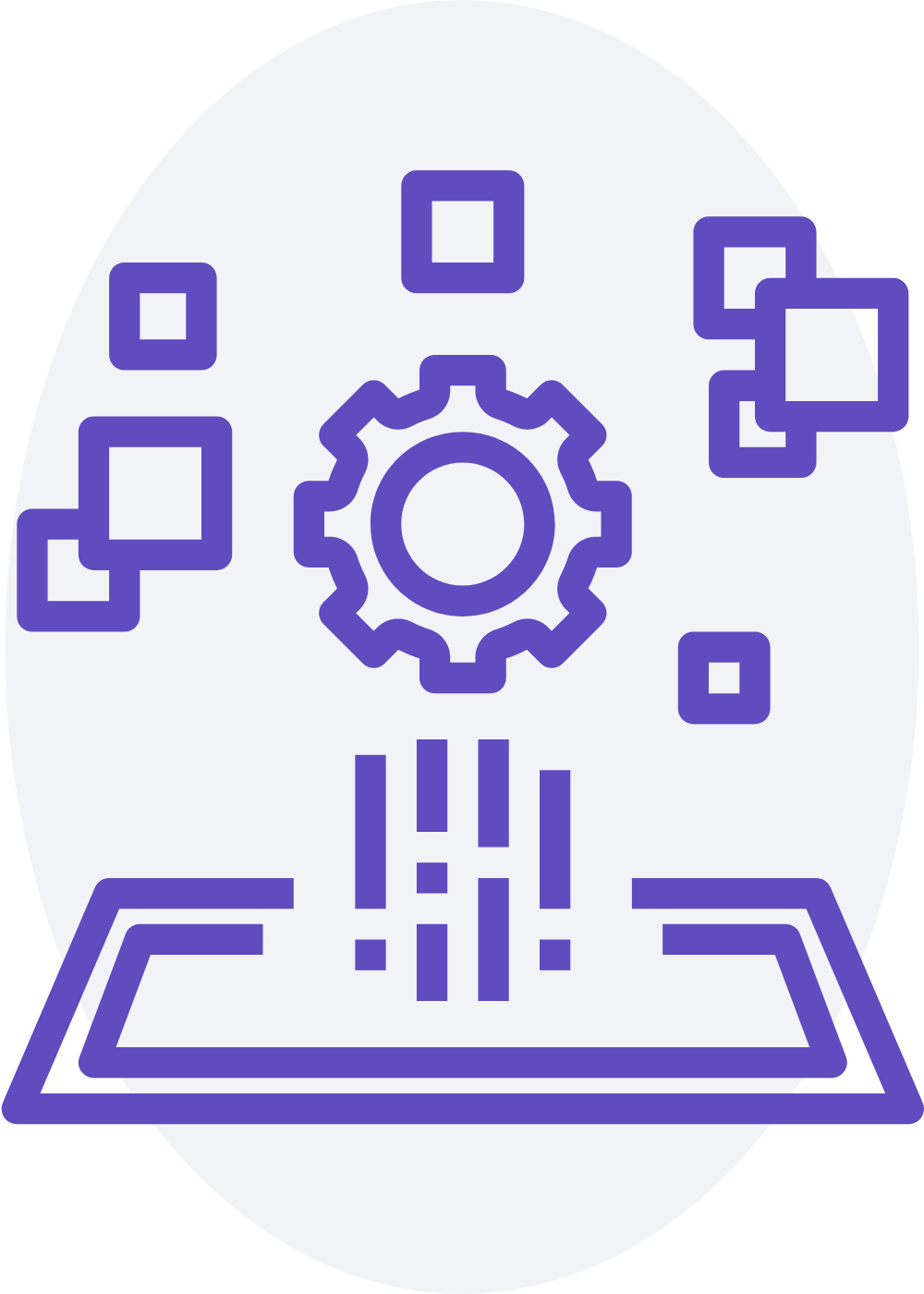
Advanced Sterilized Products (ASP), the global leader in developing innovative sterilization and infection prevention products, had six separate quality management systems before implementing Propel QMS. Once they consolidated all that functionality into one unified solution with Propel, the solution is now the hub for all ASP quality system data and records; including product lifecycle management (PLM), supplier management, QS training, document control, CAPAs, non-conformances, calibration & maintenance, customer complaints, and audit observations. Read ASP’s story.
Streamline Review Processes – From 5 Days to 5 Minutes
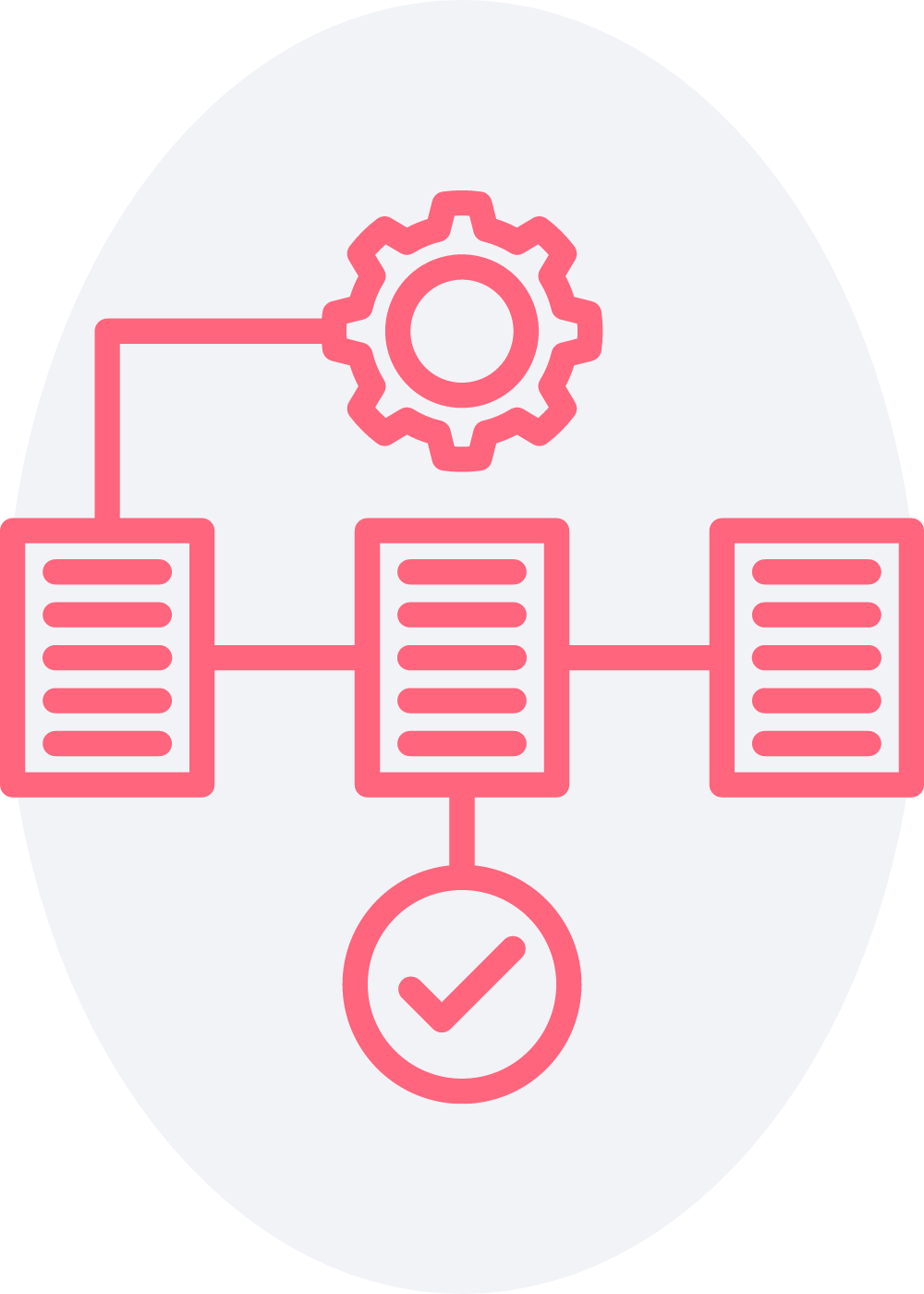
Imperative Care is dedicated to improving the way stroke is treated by advancing medical technology, and therefore improving their quality management processes as well. Propel’s comprehensive dashboards and reports have enabled Imperative Care to spend less time on administrative work and more time creating life-changing products for their customers. “At a moment’s notice, we can see the pulse of where our quality system lies. My management review process has gone from five days of data crunching and analyzing graphs and spreadsheets to a 5-minute report and I’m done,” said Donielle Boudin, Director of Quality. Read Imperative Care’s story.
Speed from Complaint to Resolution
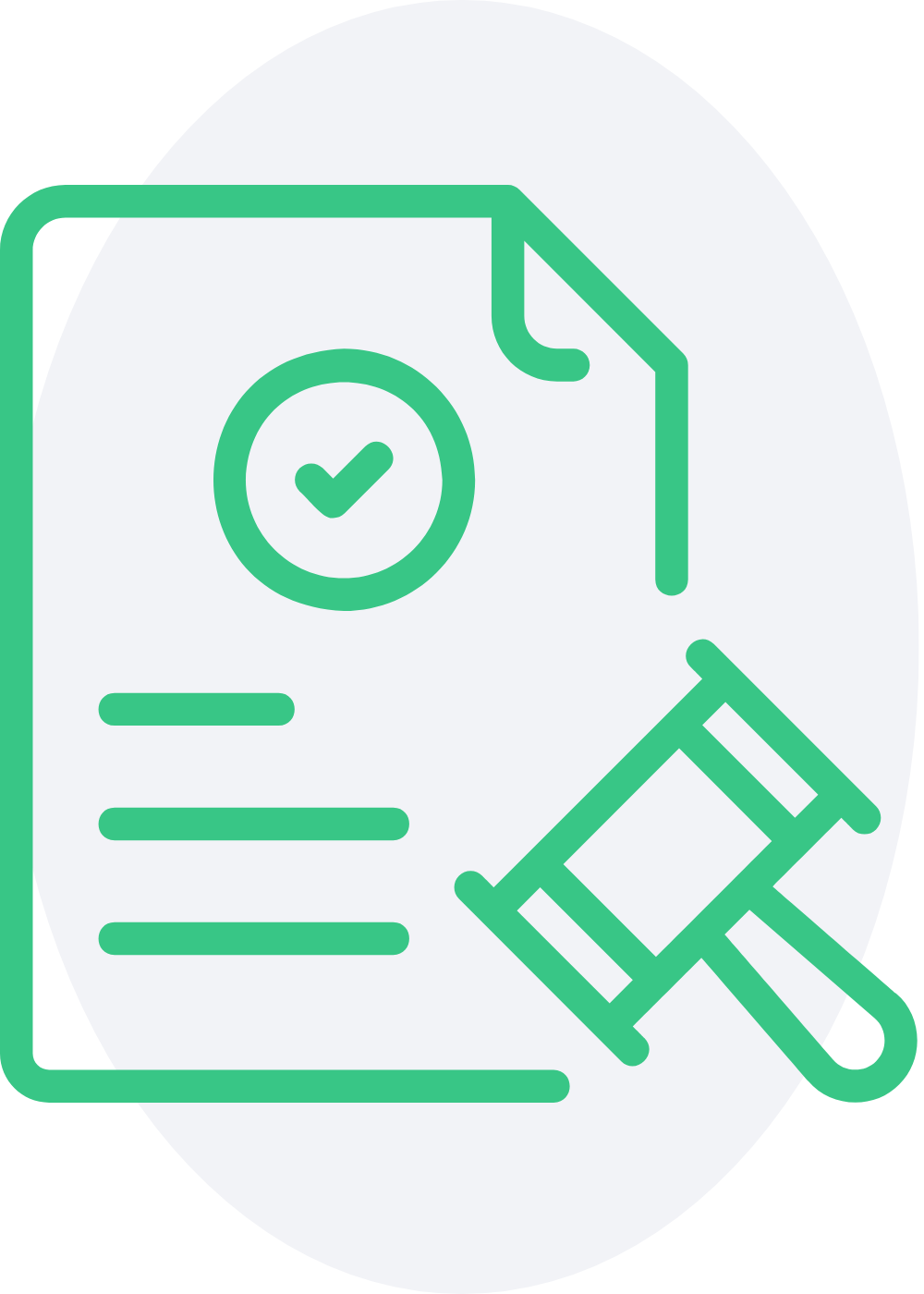
Axena Health, a women-led enterprise dedicated to transforming lives with their groundbreaking Leva Pelvic Health System, needed a QMS that provided the speed they needed to quickly pass audits. They selected Propel QMS because it facilitates rapid handling of complaints. By leveraging Salesforce’s case form functionality, Axena efficiently feeds complaint records into Propel (a Saleforce-native solution), ensuring a continuous product thread. This integration fosters seamless automated workflows and enterprise-wide collaboration. Consequently, Fitzgerald’s team can quickly act on customer cases, comply with FDA MDR reporting, and address potential adverse events and defects promptly. The system’s smooth operation and real-time visibility into issues empower them to take swift action, preventing delays and ensuring timely resolutions. Read Axena Health’s story.
Conclusion: The Essential Role of Propel QMS in Continuous Improvement
Propel QMS is essential for driving continuous improvement within an organization due to its unique offering as the only solution that connects QMS with Product Lifecycle Management (PLM) and Product Information Management (PIM) all on a single cloud-native platform. The comprehensive solution offers end-to-end visibility, enabling seamless collaboration and real-time updates across all stages of product development, quality management, and commercialization.
By utilizing Propel QMS, organizations can effectively identify and address bottlenecks, manage cycle times, and implement small, incremental changes with greater efficiency. The platform's robust process management capabilities foster teamwork and ensure that all team members are aligned and informed. Propel's holistic approach to combining PLM, QMS, and PIM empowers companies to sustain continuous improvement, driving long-term success and competitiveness in a rapidly evolving market.