If you’ve been in the quality game for the past few decades, you probably know the name MasterControl’s Quality Management System (QMS).
MasterControl has built a reputation for helping medical device and health and life sciences (HLS) companies streamline their document control and maintain regulatory compliance for core activities like meeting regulations, standards, audit management, CAPA (corrective and preventive actions), and quality event management. The software company’s success stems from their ability to provide a structured approach to quality processes, so HLS companies can focus more energy on designing life-changing products.
Today, however, the same structure that once fueled MasterControl's success is now its greatest limitation.
A House of (Info)Cards
At the heart of MasterControl’s system is a foundational object called the InfoCard, a copied template for various forms and documents, constantly repurposed for quality events, components, and suppliers. This allowed for basic consistency and control—essential for industries like pharmaceuticals and medical devices navigating EU and ISO standards, or stringent requirements of the FDA and other regulatory bodies.
But the industry has evolved to become more complex, and so have the needs of QMS users. Fast-moving companies don’t view QMS as a standalone collection of processes, but rather as an integral part of a complete product record that spans from concept to customer. Today, companies require more than just document control; they need systems that are configurable, scalable, and integrated with the broader ecosystem of product development and supply chain management.
Under the strain of meeting the demands of these fast-moving companies, InfoCards have several intrinsic challenges and limitations. They're rigid, meaning users are typically forced to follow their process as designed, without the option to configure the InfoCards to their growing needs. Any extendibility often requires costly professional services to customize fields, reports, and processes to be compatible with upstream and downstream solutions.
Without intuitive connectivity or flexibility, MasterControl users are hampered by inefficiency, traceability challenges, and risk missing critical information during audits or investigations.
All this to say, MasterControl’s reliance on simplicity, such as their rinse-and-repeat use of the InfoCard, has turned into a liability in this new era:
A house of cards that may soon collapse under the weight of modern demands. MasterControl’s InfoCard structure is just one of the many useless features you don’t need but still have to pay for.
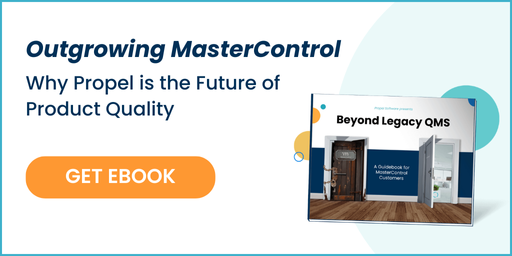
1. Configurability Challenges
At its core, MasterControl is a rigid system. While its approach of standardized forms and documents brought uniformity, it also imposed limitations that are increasingly difficult to overlook.
Every entity—whether it’s a change request, a quality event, a supplier, or even a component part—is essentially just another InfoCard, with limited distinction in meaning, differentiation, or capability. When everything is boiled down to a generic object, it becomes nearly impossible for a company to customize workflows, reporting, or data fields in a way that accurately reflects the specific requirements or validation needs of each process. Instead, companies are forced to hire third-party coding services to extend or configure the system to meet their specifications.
Users are stuck with what they have, and any attempts to modify the system to better fit evolving business processes often result in delays and frustration.
In some cases, companies reverted to managing their processes manually in Excel because MasterControl’s limited approval functionality and rigid workflows are more of a hindrance than a help.
Circumvention like this is the ultimate death knell for a software solution—not only signaling a failure to meet its own functionality claims, but also leading to inefficiencies, errors, and IP security risk.
Business Impact:
- The Approval Matrix is set in stone, making it difficult to automate and adapt to organizational changes.
- Reports are limited in scope, preventing users from generating the insights they need.
- Workflows for everyday quality tasks such as change control or nonconformance reports are not easily modifiable, stifling innovation and efficiency.
2. Scaling Limitations
MasterControl’s overly simplistic structure—including its overreliance on simple building blocks like the InfoCard—has serious implications for scalability.
MasterControl’s vault system, which controls permissions and lifecycle phases, exacerbates this problem. To enable access to InfoCards across different product types, lifecycles, parts, and components, administrators have to continually create new vaults, further complicating the system while increasing the administration burden and user experience.
Each new product variation, each new type of document or process, all demand the creation of more and more vaults. This approach quickly becomes unwieldy, making it nearly impossible to maintain a coherent system as the business expands.
As more cards get added to the pile, the foundation becomes shakier. Suddenly, companies find themselves in an administrative nightmare with severe limits on the system’s ability to scale.
By contrast, a modern QMS architecture is designed to scale effortlessly, allowing businesses to manage increasing complexity with ease. It supports seamless integration, flexible configurations, and a dynamic approach that grows with the company's size and needs, ensuring that quality management remains robust and responsive, no matter how large or diversified the operations become.
Business Impact:
- Managing multiple product variations requires the creation of excessive InfoCards, leading to system bloat.
- The vault system creates silos wherein data and processes created by one team cannot be easily shared with others, hindering collaboration and efficiency.
- The software struggles to scale as business needs grow, making it unsustainable for large or rapidly growing companies.
3. A Standalone System
In the modern day of quality management, you can’t play solitaire. Any eQMS technology offers limited value without connection to the entire product lifecycle because most quality issues ultimately need to be remedied with a product or supplier change.
While MasterControl also offers MES, its design as a standalone document management system means it lacks the ability to connect seamlessly with product data, supply chain information, and other critical business functions.
If your standalone QMS tracks a problem that necessitates collaboration with product development, get your swivel chair ready because you’re in for a lot of switching back and forth between systems.
Needless to say, this time-consuming and error-prone manual data entry runs counter to the speed of the modern market, let alone the risk management needs of today’s unpredictable supply chains.
For example, when a significant quality issue arises—like a deviation that requires escalation—it’s crucial in these scenarios to trace the problem back to its source as soon as possible. These sources could be a component supplier, sub-assembly, part, or manufacturing process – all information that’s typically housed in product lifecycle software.
MasterControl’s system, with its rudimentary Bill of Materials (BOM) and lack of integration with ERP systems, makes this process cumbersome at best and impossible at worst.
The absence of basic traceability for product details—i.e. Where Used, Where Sold, Where Sourced, etc.—due to the InfoCard architecture severely limits the ability to easily find and replace affected parts across multiple products or processes. The result is a disjointed approach to quality that fails to close the loop between product development, production, and quality control.
Business Impact:
- The BOM functionality is underdeveloped, lacking depth and integration with supplier and product data.
- The system is reactive rather than proactive, unable to support closed-loop quality processes that are essential in today’s complex manufacturing environments.
- Lack of traceability for basic product details such as Where Used makes it difficult to address quality problems before they arise (or before a product ships)
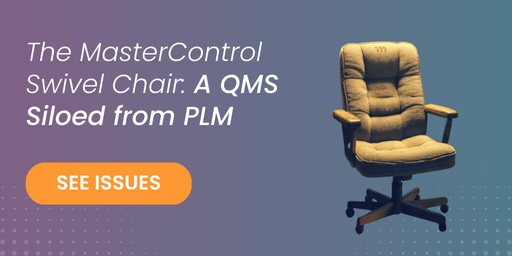
4. On-Prem in a Cloud Disguise
As cloud-native solutions rapidly become the norm, MasterControl’s approach to cloud computing falls short. Akin to an on-premise solution with a cloud interface—MasterControl’s model fails to deliver the full benefits compared to a software system that was built on the cloud from day one.
Cloud-native software is optimized for elastic scaling, built with distributed resources and services (enhancing fault tolerance and reducing downtime), and facilitates continuous integration and deployment.
On the other hand, MasterControl’s on-premise-turned-cloud approach comes with significant drawbacks. Scaling is limited by the original design of the legacy system, and integrating with other cloud-native services may be more complex and require additional adaptation work.
Innovation is also stifled, as the MasterControl single-tenet model limits the ability to share updates and new features across users. Not to mention MasterControl on-prem support retires in 2025.
Additionally, the lack of essential functionalities that are table stakes for cloud-native solutions — like global search, customizable reporting, no-code/low-code composability, and a user-friendly interface — further diminishes the value of their cloud offering.
Business Impact:
- Missing basic cloud functionalities, such as a global search engine and flexible reporting, can hinder process automation and efficiency—and box businesses out of their market.
- Hosted cloud offerings fail to deliver the performance and scalability of cloud-native solutions. For example, non-cloud native applications often can’t handle data transfer and storage efficiently across distributed networks, resulting in higher costs and slower access times that impact overall performance.
- The single-tenant model limits innovation and increases costs, requiring separate infrastructure for each client — leading to duplicated resources such as hardware, storage, and networking capabilities. Not to mention individual costs of custom maintenance and updates.
The House of Cards is About to Collapse
For businesses looking to not just maintain quality, but continuously improve product quality in a cost-efficient manner, it's time to look beyond MasterControl.
When MasterControl first arrived on the scene, it was a big step up from paper-based processes.
But for the modern landscape of regulated industries, it’s risky to rely on older infrastructure for high-stakes regulatory activities, especially in the era of disruption. If the quality management software isn’t natively built for cohesive collaboration and real-time information access, no amount of third-party code updates can create the speed required.
MasterControl’s basic structure has served them well in the past, but the modern QMS landscape demands it be directly connected to PLM. Companies have increasingly complex needs and therefore require software systems that are configurable, scalable, integrated, and truly cloud-native.
MasterControl’s inability to evolve beyond its original architecture has left it vulnerable, and the cracks in their foundation are becoming increasingly difficult to ignore.
Try a House Built to Last
Propel Software offers an eQMS built for the future. Unlike MasterControl’s rigid system, Propel’s eQMS software solution is fully integrated with product lifecycle management (PLM), highly configurable, and scalable so it grows with you as your company size and complexity grows.
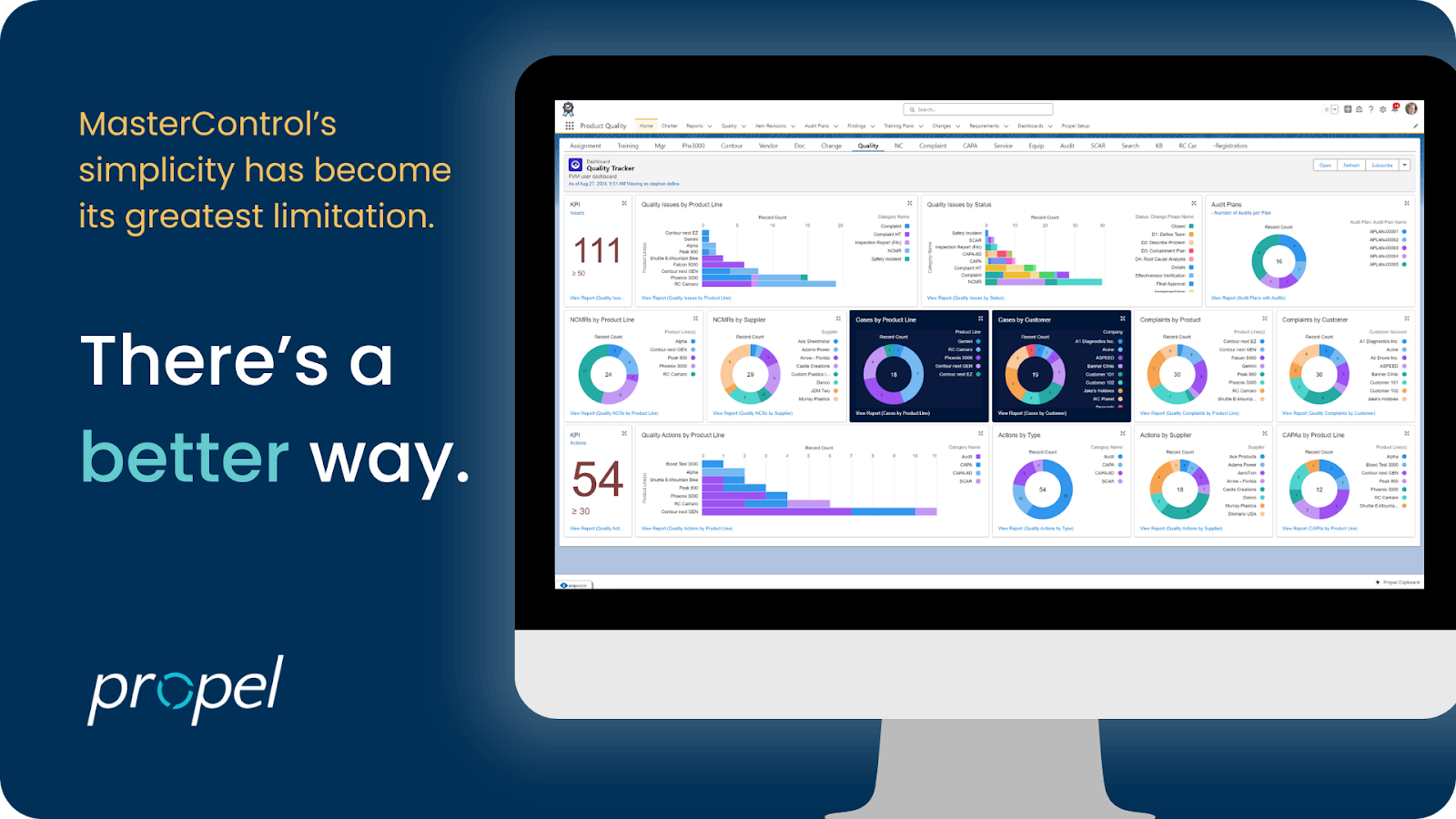
It’s designed to evolve with your business, ensuring that compliance is a natural outcome of your processes—not an afterthought.
With Propel, you’re not just managing documents; you’re managing your entire product lifecycle, from design and production to quality control and customer support. Propel’s modern, cloud-native platform provides real-time reporting, automated training tasks, fully structured BOMs, customizable workflows, and a seamless user experience, making it the ideal solution for companies looking to stay ahead in today’s competitive landscape.
The house of cards is falling—don’t let your business go down with it. Make the move to Propel and build an eQMS that’s as dynamic and resilient as the products you create.