NBC News recently reported that 1.6 million manufacturing jobs were reshored to the United States since 2010, including 350K in 2022 alone. The acceleration in recent years was caused by what is now a familiar story: the supply chain shocks caused by the pandemic created demand for local suppliers that are less likely to be interrupted by unexpected events.
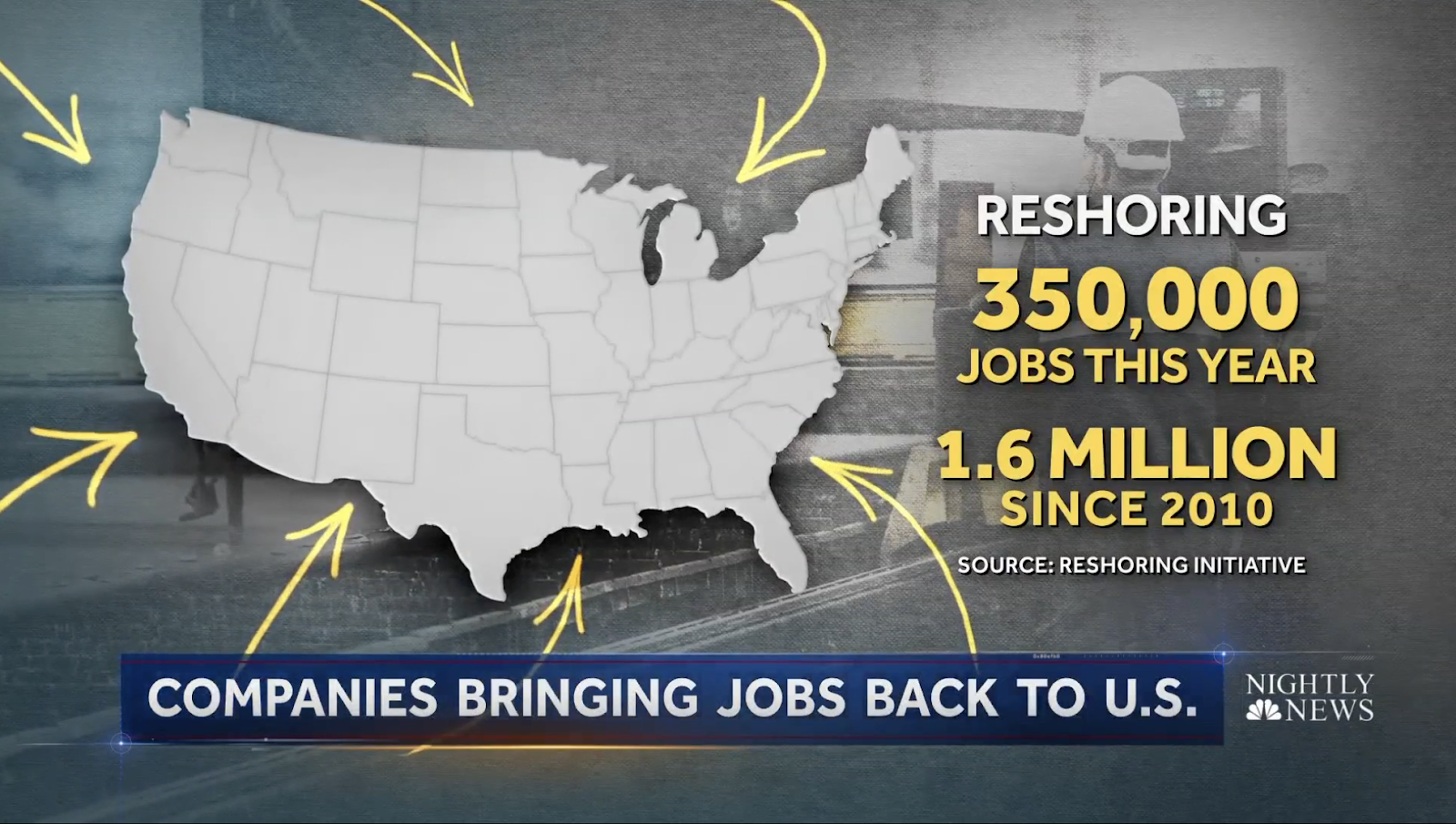
Over the past few years, we’ve seen Just In Time inventory management replaced with Just In Case as supply chain leaders followed through with their plans to invest in supply chain resilience.
Outside of the obvious benefits of more local jobs and training for the next generation of manufacturing workers, rebuilding a manufacturing base in the US creates more options for domestic manufacturers.
These manufacturers need to ask the right questions to determine which supplier and partner strategy is right for their needs.
Local Supply Chains as a Strategic Advantage
Shifting supply chains are not new. Decades of domestic manufacturing jobs followed a similar pattern of globalization where production was systematically moved to lower-cost countries to gain a competitive advantage on pricing. This did not always result in a one-way flow of jobs leaving the country.
Take the example of the automobile industry, where Japanese and German manufacturers took big chunks of market share from domestic brands and then established manufacturing operations in the United States to reduce shipping costs, remove currency risk and take advantage of a highly skilled labor force.
The pandemic showed the risk of always chasing the lowest-cost supplier.
What happens when a supplier is in a region or country where the local government has a propensity to shut down operations on a whim?
What happens when a supplier relies on transportation that comes to a halt when a ship runs aground in a global bottleneck?
What happens when wars interrupt production or an earthquake hits a key supplier or a hurricane damages vital transportation infrastructure?
The greater the distance between suppliers and end manufacturers, the greater the chance that one or more of these challenges—not to mention many more—will impact a company’s ability to deliver a finished product to their customers.
Since customers are not keen to pay for a product that is not finished, distributed global supply chains can provide a real risk to a company’s very existence.
There are more advantages to local supply chains than risk reduction:
- Local suppliers can pair flexibility with shorter delivery times, which can be a huge competitive advantage when building custom-engineered products.
- Those shorter delivery timelines can also speed time to revenue and increase pricing power by helping get products to market faster.
- And local suppliers can have a better understanding of local regulations and sustainability requirements, as well as local preferences.
That’s not to say global suppliers cannot be competitive in these areas. It’s just that local suppliers add options that should be part of the decision process for manufacturers.
Local and Global Supply Chains
The decades-long trend of searching for the lowest-cost suppliers has introduced a lot of risk to global supply chains. That’s why many experts have recommended for years that supply chains remove any single-threaded sources to create redundancy. Best practice calls for redundant suppliers to be located in different geographic locations to mitigate the impact of any local interruption.
And yet, most companies did not build these redundant and resilient supply chains.
Some because they did not see the need. As long as their customers demanded low-cost products, their single focus remained on low-cost suppliers. Others because managing multiple suppliers is complex. Why make the effort to diversify if you are just going to default to the low-cost supplier?
That all changed over the past couple of years and local suppliers are now providing more options to consider.
Manufacturers need to ask what is truly important to their business and customer base. Is it speed to market so customers have the newest products faster than their competitors? Reduced risk to increase the probability of consistent product availability? Lowest cost to meet the needs of price-sensitive buyers?
Answering these questions will help manufacturers determine their ideal supply chain strategy, which in turn helps determine the proper mix of local versus international suppliers.
The past few years have also seen a big increase in supply chain technology, which can also be leveraged to increase resiliency.
Better insights into customer demand and market trends improve the efficiency of supply chain and inventory management, which helps reduce waste, lower costs, and positively impact sustainability.
Supply chain data intelligence reduces risk and increases profitability by providing insights into component availability, cost, and sustainability scores. These insights can help manufacturers avoid problems before they arise.
Manufacturers are also increasingly investing in technology that improves responsiveness. Although we can do our best to build resilient supply chains, none of us can predict the future. We know that unexpected events and shocks will take place, but we don’t know where, when, or the full impact of those events. That’s why visibility, collaboration, and flexibility are also important elements of a resilient supply chain strategy.
Supply chain reshoring is a great trend for manufacturers because more choices increase the chances of finding the right partner. Manufacturers should determine what’s important to their business, understand their customers’ needs and invest in technology that improves their supply chain flexibility. The right mix of local and global suppliers will naturally follow.
Consider other ways of increasing the flexibility of your supply chain and decreasing risk, such as building a more robust criteria for supplier management.