Evolution is the new constant.
If this doesn’t resonate with you, you may not be involved in the manufacturing industry. Well, believe me, it’s a good time to hop on board.
Right now, we’re in what’s commonly known as the customer-first revolution, which speaks to the manufacturing industry’s requisite to evolve to meet new customer demands and to maintain competitiveness with flexible agility.
With broad changes to how business is conducted across the entire manufacturing industry, naturally, the job market is bound to evolve as well.
Consider a comparative example from history: the Industrial Revolution. As we all know, the advancement in manufacturing technology created a boom in industrial products and related jobs.
Cut to today. There have been huge advancements in technology that spawned more efficiencies in manufacturing and, contrary to popular belief, led to another boom in jobs.
Where is the manufacturing job market now, and how are companies meeting those needs? We break it down below.
Recent Trends in the Manufacturing Job Market
Over the past few years, the job market as a whole has changed drastically. In the manufacturing industry specifically, unprecedented supply chain disruption led to seismic shifts, leading manufacturing companies—and therefore manufacturing jobs—to experience hefty effects from each of these global trends:
Pandemic-Related Job Losses
The effects of the COVID-19 pandemic are still pervasive throughout the industry to this day, years later. Most, if not all, industries are still working on their recovery in 2022. There have been lasting effects, such as the sharp rise of digital commerce, that will become a permanent part of how business is conducted.
Manufacturing was bluntly impacted in regard to both the production process and to day-to-day workflows. Approximately 1.4 million U.S. manufacturing jobs were lost at the beginning of the pandemic, according to the National Association of Manufacturers. Back when there was nothing but uncertainty in the spring of 2020, companies unsurprisingly responded with a pared-down workforce.
The good news is product companies have been filling these openings over recent years. Much like the industry itself, many of the open jobs have shifted to address the new role of technology in the production process.
The Great Resignation
Coming on the tail end of company shutdowns and a return to relative normalcy, the manufacturing industry, among others, has seen a large spike in attrition rates—a phenomenon many know as the “Great Resignation.”
The Washington Post reported that this phenomenon has hit the manufacturing industry harder than any other industry with a 60% increase in resignation rate when compared to pre-pandemic numbers. The American Society of Mechanical Engineers noted that many employees either moved or decided to pursue a new career.
In a trend consistent with virtually every other industry, reasons for this pattern included a desire for work-from-home positions and for a better work environment, culture, and fit.
As expected, the “Great Resignation” did not just have an effect on hiring practices, it changed the manufacturing of products itself and even the greater supply chain.
The silver lining? This shake-up forced companies to retool their ideas of workplace norms, creating an opening for a new type of job within the manufacturing sector.
Inflation
Manufacturing industry leaders are feeling it everywhere. Significant economic changes, especially depressive ones, trickle into every part of the supply chain process. Some critical aspects of supply chain expenditure most impacted by inflation include—
- Increased Material Cost
- Increased Storage Cost
- Increased Transportation Costs
- Decreased Customer Buying Power
When these factors are severely strained, there’s bound to be a tangible effect on a manufacturing company’s budget and therefore on employee’s wages.
And as we all know, there’s often a lag between an increase in the cost of living due to inflation and an increase in wages. Which, in turn, affects the job market and employees readily available in the workforce.
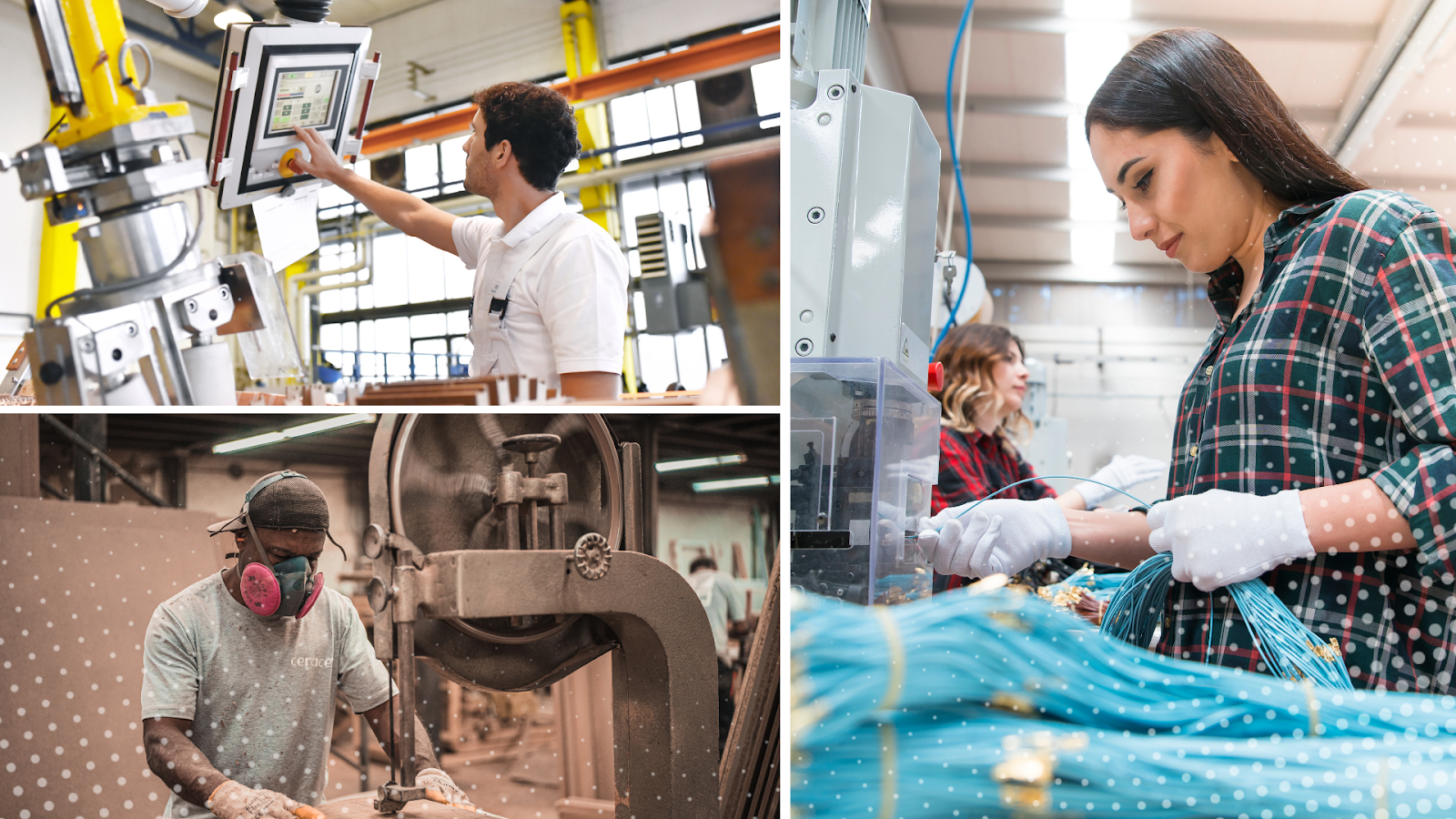
Digital Transformation of Manufacturing
Okay, so what’s the good news?
With all of these shifts in business practices and workforce desires, manufacturing companies are, by necessity, obliged to helm the forefront of new technology.
Though technological advancements may change how business is done, modern manufacturing businesses still have the same goals: increase production, maintain and improve the quality of products, and increase efficiency throughout the entire process.
The good news for manufacturing job seekers is that this advent of new technologies provides new ways to achieve these goals—and more job opportunities within the manufacturing space.
When we look at the traditional manufacturing workforce, like an assembly line, a common misconception is that the rise in electrical equipment, automation, machine learning, and other technologies would limit jobs.
In fact, these technologies actually create jobs and provide paths for career advancement. How?
New manufacturing equipment on the production line, such as CNC tables and robotics, require more machine operators and maintenance staff.
Plus, high-tech changes go way beyond the manufacturing floor. Advancements in technology apply to all steps in the manufacturing process. And it’s all thanks to another huge revolution in the industry dating way before the pandemic: digital transformation.
Technology in Product Management
Digital transformation begins at the very start of the product management process. Every step along the product journey requires accurate information in real-time for smooth product operations, such as raw material costs and any disruptions within the supply chain.
This is what makes tech in product management so important. Cloud-based tech streamlines communication between all points in the supply chain process.
Being able to operate within a centralized source of truth for all product information—from new product design to market performance—does much more than optimize operational efficiency, it ultimately results in greater customer satisfaction and therefore revenue growth.
With advancements in product management practices, the role of the product manager is evolving. They now need to have greater digital fluency and understand big data analytics to apply their findings. This could even mean the emergence of an entirely new job title, such as Chief Digitial Officer (it’s a thing!).
Technology in Cross-Functional Teams
If you’re doing it right, digital transformation should touch every member of every cross-functional team. When done well, companies won’t be the only ones who see the benefits of digital transformation—customers will, too.
In a survey by Propel and Acceleration Economy, 75% of IT leaders noted that their product and customer-facing teams don’t collaborate effectively. Increasing connectivity between teams provides a better experience for both team members and customers.
Single platform solutions not only optimize the communication of product information but also help to combat the business risks associated with inflation.
Not to mention the savings on Total Cost of Ownership (TCO) when you consolidate your quality, product development, and commercialization processes all into one extensible, collaborative platform.
Applying Technologies to Manufacturing Operations
When considering a cloud-based system, whether you have small or large-scale manufacturing operations, it’s important to find the right one for your business. For instance, automotive productions will have different considerations than building material companies which will have totally different needs to transportation equipment manufacturers.
Regardless of the scale and specifications of your business, companies must also ensure their workforce is trained to efficiently use the new technology.
Training and continuing education courses are important initiatives for companies to not only increase their production but also create a sustained workforce.
Providing a way for manufacturing associates to gain new skills allows employees to advance their job trajectories and have long-term careers within the manufacturing space.
Read more about recent trends in the manufacturing job market, such as the manufacturing skills gap—what is it and how can we solve it?