If your QMS is stuck in a silo, so is your team’s potential to innovate.
For companies relying on MasterControl, that's often the reality. Though they call it “MasterControl Quality Excellence,” the system is primarily designed to handle the basics of quality management software like audit management and document control.
Meanwhile, its siloed design creates significant challenges for IT leaders and product teams who are tasked with working with quality teams while staying on top of their delivery deadlines.
Here’s the truth: a standalone quality management system can’t deliver on the promise of closed-loop quality unless it’s integrated with the PLM.
Let’s explore why disconnected systems are a major downside for businesses in regulated industries, particularly life sciences and medical devices, and how they undermine the agility, traceability, and efficiency modern markets demand.
The Problems with a Standalone QMS Like MasterControl
1. A Reactive, Not Proactive System
Quality issues don’t exist in a vacuum—they’re inherently tied to product design, supplier performance, or manufacturing processes. While MasterControl QMS offers tools for standard tasks like nonconformance tracking and regulatory compliance, its siloed nature limits its ability to be proactive.
Quality issues don’t exist in a vacuum, yet standalone QMS solutions like MasterControl often limit your ability to proactively manage quality challenges. Here’s why:
- Tracking a quality event often requires data from product development or supplier management systems, which are housed separately in PLM.
- Resolving issues tied to a Bill of Materials (BOM) or component source demands tedious, manual cross-referencing between disconnected systems.
- Proactive quality improvement initiatives require historical data from PLM—such as defect patterns or supplier performance metrics—to make informed updates to designs or processes.
- Risk assessments and mitigation plans depend on access to material specifications and sourcing details in PLM, which are unavailable in standalone QMS systems.
Without integration, quality management becomes reactive and inefficient, leaving your team to address problems only after they’ve escalated.
Instead of streamlining quality processes, you’re left with time-consuming data entry and constant context switching. And in industries like pharmaceuticals or medical devices, where FDA oversight demands real-time accuracy, delays can be costly—or even catastrophic.
Beyond just being siloed, MasterControl has several features that leave users frustrated. This article breaks down six aspects of the system that don’t make sense.
%20Converged%20Banner.png)
2. Traceability Gaps and a Lack of Closed-Loop Quality
Traceability is at the heart of quality management in regulated industries, yet MasterControl Quality Management System falls short due to its limited ability to connect product and quality data.
Consider a scenario: A deviation in a manufacturing process necessitates an escalation. To address it, you need to trace the issue back to the affected supplier, component, or part. With MasterControl’s rudimentary BOM functionality and lack of ERP integration, this process becomes a manual slog.
A siloed system makes traceability—the foundation of quality management—an uphill battle. When software systems don’t communicate, it’s impossible to connect the dots across the product lifecycle. For example:
- Root cause analysis for deviations or nonconformances requires design history and engineering records housed in PLM, making issue resolution a manual and error-prone process.
- Product recalls or field corrections demand instant insights into affected products, including where they were used, sold, or sourced—information typically managed in PLM.
- Supplier performance evaluation requires qualification records and historical data from PLM to identify whether the source of the problem lies with a specific vendor.
- Closing the loop on CAPA (Corrective and Preventive Actions) is impossible without PLM integration, as resolving quality events often involves product or supplier changes.
Disconnected systems create blind spots that prevent businesses from achieving true closed-loop quality, exposing them to regulatory risks and operational inefficiencies.
The inability to quickly determine Where Used, Where Sold, or Where Sourced for affected parts means businesses risk missing opportunities to prevent problems before products ship. Instead of preventing quality issues, your team is stuck reacting to them.
3. Cumbersome Workflows and Inefficient Processes
Modern businesses need software solutions that eliminate friction, but MasterControl’s architecture creates its own hurdles. The InfoCard architecture limits the system’s capacity to handle detailed product or supply chain data.
As a document management system, MasterControl does the trick. However, the system falters in streamlining workflows across product and quality processes. Consider these challenges:
- Change management processes depend on PLM integration to align product updates, engineering change orders (ECOs), and design revisions with quality requirements.
- Compliance tracking with ISO or FDA standards demands consolidated reporting and traceability across product and quality records—an impossible feat for siloed systems.
- Audit and validation processes require seamless connections between product development documentation and quality workflows to avoid costly oversights and ensure regulatory readiness.
- Training tasks and document control workflows, though comprehensive, don’t integrate smoothly with product life cycle tools.
These disconnects aren’t just annoyances—they’re risks. Paper-based processes and redundant data entry introduce human error, slow audit management, and complicate validation for ISO or FDA standards.
And for companies still relying on MasterControl’s on-premise system, an even bigger disruption is coming. With MasterControl ending support for on-premise deployments in 2025, organizations will need to reassess their quality management strategy sooner rather than later. Read more about the implications here.
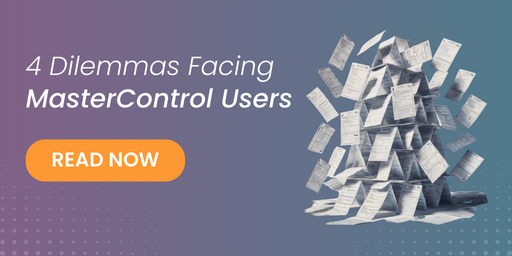
The Business Impact of Disconnected Systems
The costs of running a siloed QMS extend beyond inefficiency. Let’s look at the tangible impacts on your business:
Stalled Innovation
Disconnected systems make it harder to align quality processes with product development timelines. This slows the delivery of life-changing products and hampers your competitive edge in fast-paced markets like life sciences.
Elevated Risk
Without integration between QMS and risk management tools, your ability to identify and address potential hazards early is compromised. This is especially critical in managing deviations, preventive actions, and quality event management.
Increased Costs
Inefficiency drives up operational costs. The time spent toggling between disconnected systems could be better spent automating workflows, improving training management, or refining change control processes.
What Businesses Need Instead: A Unified Approach
The costs of operating with a siloed QMS like MasterControl are too significant to ignore. From delayed innovation to elevated risks and inflated costs, the lack of integration between quality management and product lifecycle systems hinders your business’s ability to compete in today’s fast-paced, high-stakes markets.
But it doesn’t have to be this way. Propel Software offers a modern, cloud-native eQMS built on a unified platform that seamlessly connects quality processes with product lifecycle management. Propel’s technology empowers you to:
- Close the loop on CAPA, change control, and other critical workflows with integrated product data.
- Ensure real-time traceability for quality events, design changes, and supplier information.
- Streamline and automate compliance efforts for FDA, ISO, and other regulatory standards with user-based workflows built with an intuitive, single-source-of-truth platform.
Propel’s connected solution ensures your team can focus on innovation while maintaining the highest levels of quality and regulatory compliance.