As we laid out in in Part I of this series, implementing and operationalizing total quality management (TQM) requires a deep commitment across the entire organization, with strategic planning and top management leadership. It can be a challenge for some organizations—but if you can overcome them then you’ll be on a path toward continuous improvement, greater market share, and long-term success.
We’re going to dive into the pros and cons of total quality management to provide transparency on where we’ve seen organizations struggle. Propel Software has worked with companies like Vizio, Kichler, and FormLabs, who use Propel’s collaborative, cloud-based, fully integrated solution to build compelling and profitable products, increase customer satisfaction, secure customer loyalty, and achieve high quality throughout their value chains.
Over the years, Propel has seen the pros and cons of TQM come to life within these organizations as they implemented integrated systems that increase their TQM success. Here are some of the lessons learned:
Pros of Total Quality Management:
- Deliver better products to customers - Since customers are at the center of TQM, the number one goal is to deliver stronger and higher quality based on customer-focused, fact-based decision-making throughout the value chain.
- Enhance brand image - Customers who interact with a company that truly operationalizes the principles of TQM into their business processes will likely see an increase in brand image and reputation - which can result in increased sales via word of mouth and satisfied customers.
- Less product defects - By deeply analyzing the data in each documented process, with methodical statistical process control, companies can reduce product defects early in the product development lifecycle.
- Results in lower company-wide costs - While TQM takes an upfront investment, if operationalized with full employee involvement throughout the entire organization, not just the production process, it can dramatically decrease costs in the long run.
- Minimizes product and time waste - From reducing time to market to actual costs in raw materials, TQM can save companies time and money by focusing on initiatives that bring the most value while figuring out ways to incrementally improve across all areas of the business, ultimately resulting in higher quality products and therefore greater customer satisfaction.
- Creates well-defined company values - Because TQM requires company-wide belief, this means organizations must spend time defining and continuously living up to their defined company values which means they are often more operationalized, drive effective communication, and get baked into the DNA of the company.
- Enables a company to become more adaptable to changing markets & regulatory environments - If done correctly, TQM actually enables all stakeholders at the company to detect and react earlier to changing consumer mindsets and desires. Beyond this, it enables easy adjustment to regulatory changes because all processes are already documented and methodology can easily be changed to meet customer requirements.
Cons of Total Quality Management:
- Typically requires substantial financial investment to convert to TQM - Though the cost of quality is always a major consideration, TQM is an entirely different beast altogether. Because TQM requires a holistic mindset shift, intensive project management, robust documentation across all processes, and thorough training, especially early on, it can be time and money-intensive upfront.
- Can be difficult to implement without expertise - If your organization wants to make the shift and feel the full benefits of TQM, it will require thorough education and expertise on the topic to properly implement it. That doesn’t mean you have to hire one of the big four consulting firms to get it right - but it does mean you want to have a clear plan of action and expert guidance.
- May be met with resistance to change by employees at all levels - If you’re an existing organization that has long-term employees who have been operating under a different management approach or with a lack of a clearly defined one, it can be challenging to get all stakeholders onboard. Effective communication and clarity is the best answer to this challenge.
- Will initially reveal customer dissatisfaction - When beginning to shift to TQM, some companies may feel scared to undergo this process because the new metrics will reveal flaws in business processes and areas where customer satisfaction is lacking, across all areas of the business. Instead of looking at these as failings, look at them as opportunities for continuous improvement.
- Requires ongoing feedback and training - Every business wants quick-win total quality control solutions that can easily be implemented and last forever… but that’s not what TQM is all about. It is a management tool that requires clear feedback from employees, customers, and partners with ongoing training as new learnings and process improvements are found.
- Can take years to show results - When you begin to implement or operationalize TQM, it’s critical to have a clear plan on what you hope to improve and how you will evaluate its success. Be sure you understand what you’re really trying to improve and the metrics you’ll measure both in the short and long term as an organization. Before long, you’ll not only meet but exceed customer expectations.
- Can discourage creativity and flexibility - Some companies get a bit too rigid in being data-driven and fact-based using TQM, especially in today’s fast-paced digital age. They may rely on traditional methods of quality assurance or quality control, when in reality TQM is first and foremost a methodology rather than a set of steps. Companies who implement TQM the right way find the balance of being adaptable but still very process-driven.
Unlock the full potential of your TQM strategy with Propel's advanced QMS solution. Seamlessly integrate quality processes for unparalleled efficiency across the entire organization — see a demo.
Examples of Total Quality Management in Practice
The idea of total quality management originated in the manufacturing sector, but the principles of TQM can really be used by any type of company. Because it focuses on long-term value and impact versus short-term wins, it is a great way for organizations to implement systemic change as they mature.
One of the top examples of manufacturing companies that have successfully implemented TQM and kaizen principles is Toyota. Originally, Toyota adopted a somewhat related practice called statistical quality control (SQC) in 1949. They iterated on this in 1951 with the launch of the Creative Idea Suggest System which was loosely based on a suggestion system used by their competitor, Ford. Toyota was awarded the Deming Application Prize in 1965 for their major advances in quality improvement. In 1994, the "Toyota Group Executive TQM Training Course" was established, which provided deep TQM training for all executives. They continue to utilize TQM and are a leader in how to be both process-oriented and adaptable.
Exxon implemented TQM after the Exxon-Valdez oil spill of 1989 to help them recover their brand image by focusing on the customer experience and relation to their product. This helped them improve their brand image but they have seen challenges recently as consumer mindset and regulatory environments shift.
How to Reap the Benefits of TQM at Your Company
While it’s important to assess the pros and cons with any major organizational decision—especially one that requires full employee involvement—the most important factor is how long will the identified benefits demonstrating a lasting improvement for your company? With continuous improvement at the core of the principles of TQM, you can be assured that the initial effort and cost will evidence lasting competitive results.
Explore Propel Software to see for yourself the cohesive collaboration made possible by a modern quality management system (QMS).
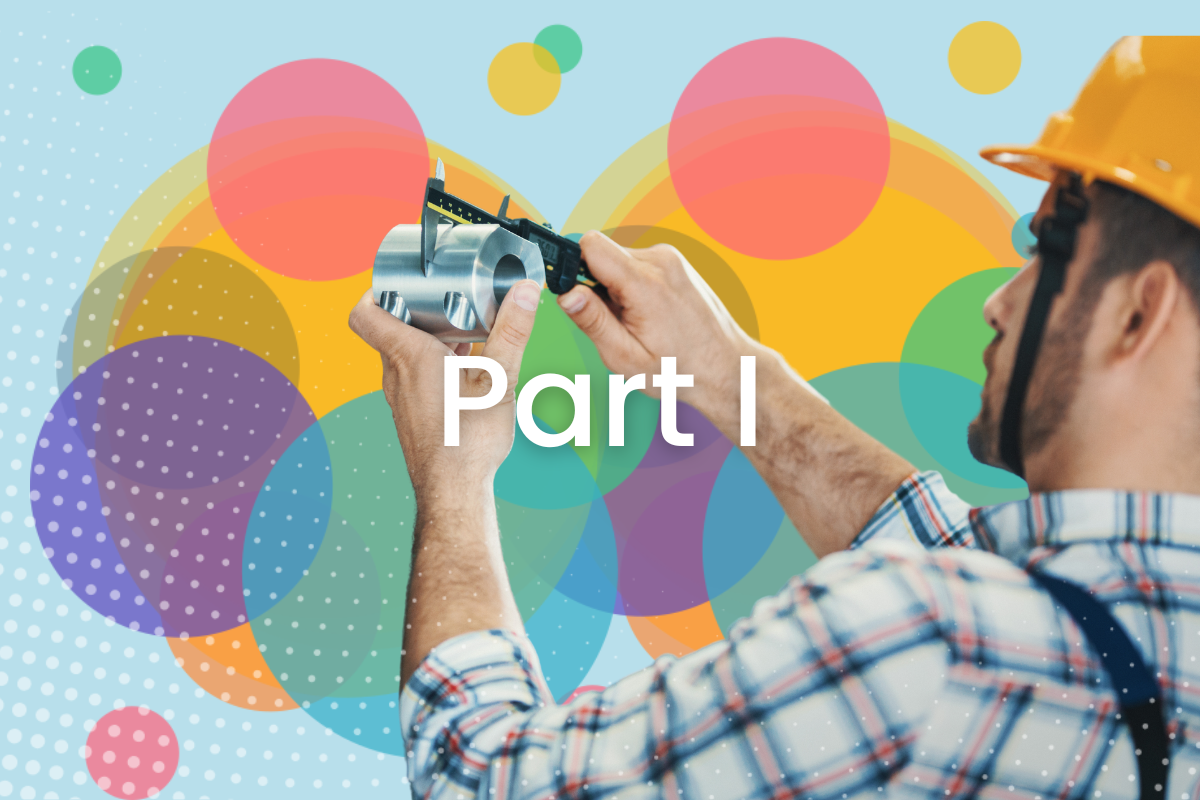
Click to read Part I: The 8 Primary Principles of Total Quality Management
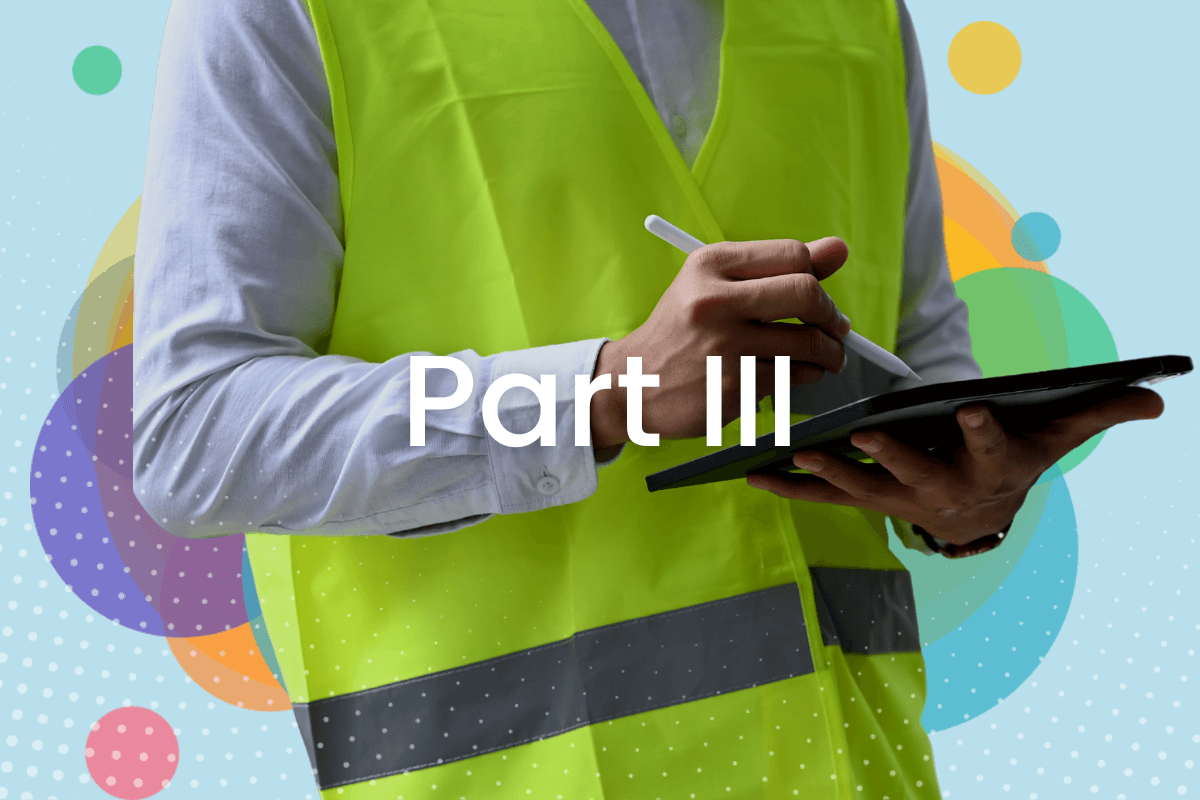
Click to read Part III: How to Succeed with Total Quality Management in the Digital Age