Now that we’ve talked all about the primary principles (part I) and pros and cons of TQM (part II), you’re probably wondering how to actually get started implementing total quality management (TQM). Or, maybe, you’ve already started down this journey but are having some setbacks and are looking at how to redirect you and your team towards a path of success.
Like most organizational changes, adopting total quality management at your organization starts with the PDCA model. While many organizations want to flip a switch and have the whole organization adopt TQM immediately, it takes a bit more patience than that.
We suggest definitely letting the whole company know about the shift and get their feedback early on. This starts to set the principles of TQM in practice while allowing you to focus on the areas that might be the easiest to improve while having the biggest customer benefits. Once you conquer that section, you can learn and iterate for the next area of the business and eventually get the whole organization on the same page.
Propel Software fuels TQM with a single product thread, extending collaboration and processes across the company, so quality teams can influence outcomes with quality best practices. Get a demo.
As you look to get started, here is the PDCA model for TQM:
- Plan - The most important phase, employees and management must come together to understand the challenges that they hope to solve with TQM. This often means identifying the day-to-day problems that management may not be aware of by listening closely to employees, partners, and customers to determine the root causes of problems not the symptoms of them. In this phase, the original process should be documented.
- Do - This is the process of implementing the proposed strategy to solve the root problem. The new process needs to be documented - and only one variable (or minimal variables) should be changed at a time to be able to accurately assess the impacts of proposed changes.
- Check - Once the change has been implemented, data should be collected and checked to see if it is having the anticipated impacts. While TQM can take a long time to holistically implement, there are early signs in success that can be analyzed and iterated on.
- Act - Once you’ve analyzed the data, you need to act on it. This might mean operationalizing the new change or actually going back to the drawing board because it had an adverse impact. If you plan to operationalize the change, the act phase also means developing the training and strategy to do just this.
Tools of Total Quality Management
There are a few basic TQM tools that allow anyone to gather data to reveal problems and potential solutions:
- Check Sheet - This is form is designed to gather one type of data over time
- Control Chart - This chart is a graphical description of how processes and results change over time based on different factors
- Pareto Chart - 80 percent of problems are linked to 20 percent of causes — and this chart helps identify which problems fall into which categories.
- Cause and Effect Diagram (Ishikawa Diagram) - With this diagram companies can visualize all possible causes of a problem or effect and categorize them
- Scatter Diagram - This diagram plots data on the x and y axes to determine how results change as the variables change to help diagnose problems
- Histogram Bar Chart - Companies use this to reveal the frequency of a problem’s cause and how and where results cluster
- Flow Chart (Stratification Diagram) - This chart shows how different factors join into a single process
While anyone can use these basic tools for free, in the internet age there are also a lot of newer technologies which help integrate systems for closed-loop product feedback. Propel’s software enables holistic product value management for manufacturing companies by connecting Product Lifecycle Management, Quality Management Systems, PIMs, and all the other tech manufacturing companies use. This helps them truly bring TQM into the digital age and allowing them to make product and company improvements faster than ever before.
Companies should also look at supplier portals/supplier management software for clear, direct, secure communication with suppliers to keep an eye on their metrics and performance pertaining to quality and regulatory standards. Supplier management is becoming more critical than ever before so fortifying supplier management while using TWM principles can really have a big impact on an organization’s future.
How to Operationalize Total Quality Management at Scale
If your organization already started implementing or has used TQM for a while now, you may be wondering how you can take it one step further.
If you’re still early-ish in your journey, but might be facing some hurdles of getting company-wide buy-in or really putting all of the principles into practice, we suggest:
- Stop and ask customers, employees, and partners - Conduct a survey in the departments where you have implemented TQM and see what’s working and what still has room for improvement. Look at each one of the eight principles as you make this evaluation.
- Go bottom-up - If you see resistance from frontline workers who are often the ones most impacted by management style shifts, think about how you can empower them. This could be implementing a Toyota style employee idea box or rewarding those employees who live the company values to show others real world examples
- Integrate it into every project - When creating a new marketing campaign, a new job description, or anything else within the company, you should have the team pause and think about how they’re integrating TQM principles and company values into the project. This can help the ideas of TQM really take hold as it requires proactive thinking from all team members involved.
- Think bigger - If you are having small-scale success, rather than thinking about the next department you can incrementally improve, think about how you can highlight the initial successes you’re seeing to get the entire company excited about TQM and thinking about what they might improve using these principles. Real world examples from other teams can help actualize vague concepts in other’s minds to help them see the true benefits of TQM.
If your company has been using the TQM style of management for a while now and it has been adopted across the entire organization, you might be facing a different set of challenges.
Some of the biggest challenges we’ve seen older organizations face is how to bring this mindset into the digital age. TQM requires robust process documentation and data-driven decision making - but to be successful today companies also need to be highly adaptable in all areas of the organization. We’ve seen how the pandemic and recent economic downturns have impacted manufacturers and customers alike - and this rapid changing environment isn’t going away.
If you’re a more mature organization who is looking to increase the success you’ve had with TQM, we suggest:
- Get all Teams to Reflect on the Past: When did your company first implement TQM? If you still have employees from around that time, they will have a wealth of knowledge. Look at the original plans for implementation and evaluate what’s happened. Get every team to reflect on how they’ve used TQM in practice and allow them to all come together to share this as a company.
- Analyze the Data & Connect the Dots: If companies aren’t integrating systems, especially in our increasingly complex supply and value chains, the process documentation and data can start to get siloed. This means that even if improvements are happening within a certain process, companies aren’t able to analyze holistic impacts and connect the dots between all areas of the business. After you get the team to reflect on the past, analyze the data across the entire organization and try to spot patterns and trends.
- Look at Your Technology & Tools: Many mature companies can get stuck in their ways—and this includes the tech and tools they use. Maybe your company adopted a QMS or PLM solution in the early 2000s or even 2010s… and you’ve never evaluated another vendor since. Legacy systems can make truly living and breathing TQM values and principles difficult because they are less integrated, often require more manual data analysis, and maintenance and updates take a long time. Doing a holistic evaluation of your technology before renewing next time can make sure you’re bringing your company along in the journey into the next phase of the digital age. A single common platform solution that integrates your QMS, PLM, and every other function of your value chain, such as Propel's product value management platform, is the ideal solution to match the power of TQM.
Explore Propel Software to find out more about the innovative capabilities of a modern, fully integrated QMS and PLM.
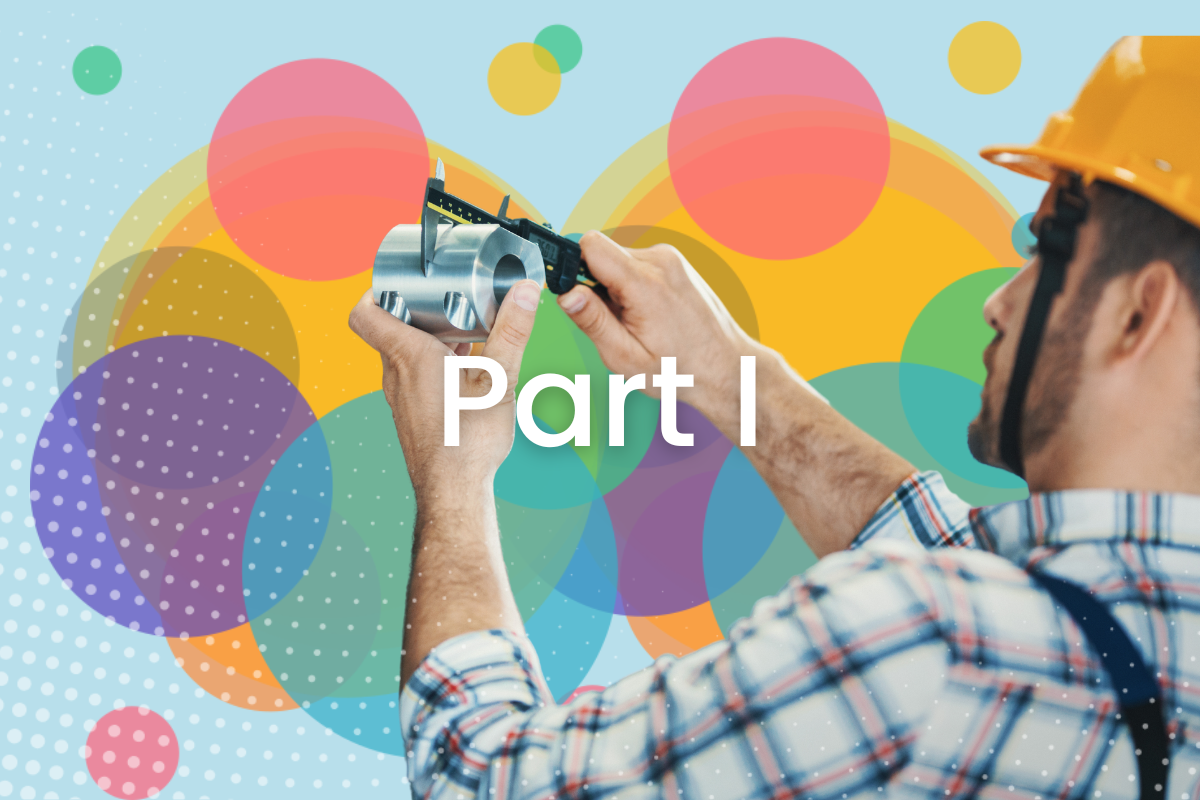
Click to read Part I: The 8 Primary Principles of Total Quality Management
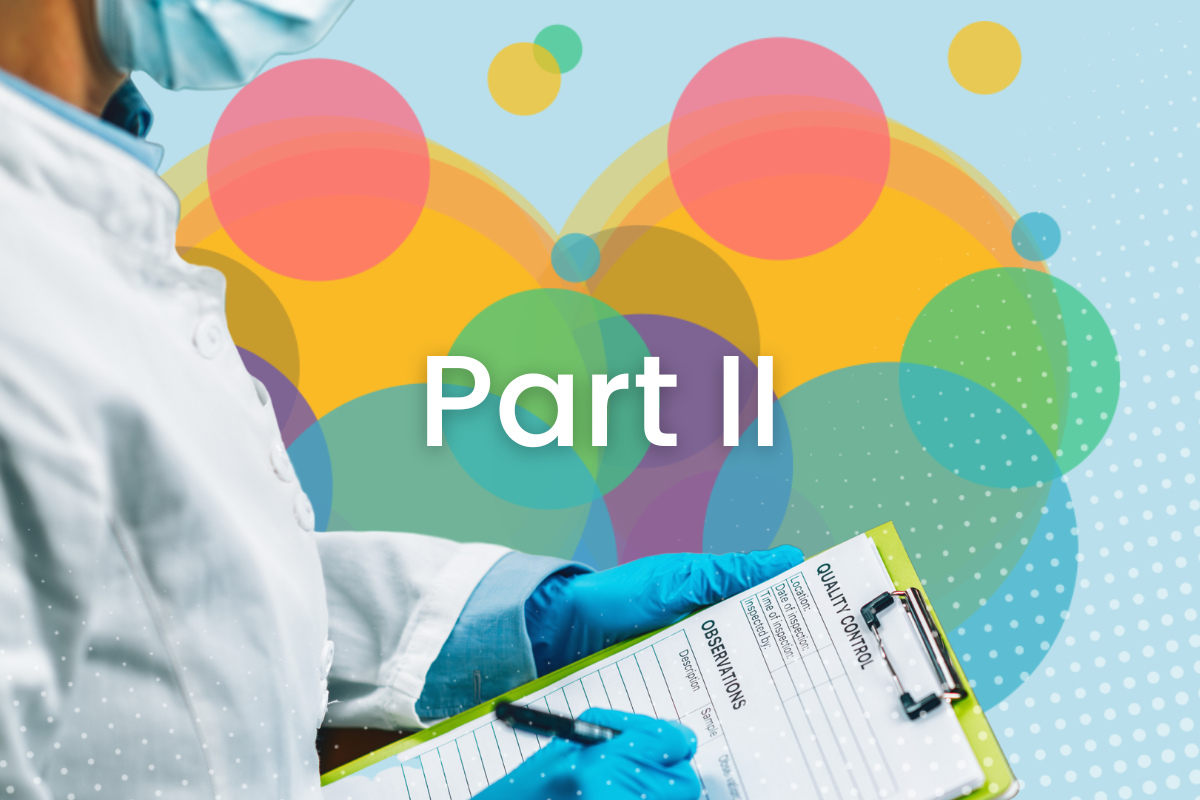
Click to read Part II: The Pros and Cons of Total Quality Management