Whether you’ve never heard of total quality management (TQM) or you’re an expert looking for the latest insights about quality improvement and methodology, stay tuned for all three parts of this series—we’ve got you covered!
With our ears open to the latest industry concerns, we found that more and more companies we talk to either use or want to use the total quality management style at their organization—so we thought we should learn more from our team and some experts on the subject to synthesize all things total quality management.
Let’s dive in!
What is Total Quality Management (TQM)?
Total quality management is a management style based on the idea that long-term success and customer satisfaction are achievable when all stakeholders commit to continuous quality improvement.
In action, this means complete top-to-bottom employee involvement. The entire organization, from new frontline workers to the highest-ranking executives, adopts a continual process of detecting and improving areas of the business by focusing on improving quality to deliver the highest customer satisfaction, and ultimately greater market share.
Every person, team, and process throughout the organization is aimed at always delivering customer satisfaction to ensure long-term customer loyalty.
Transform your quality initiatives and seamlessly align with key TQM principles with Propel's innovative Quality Management System (QMS). See a demo.
The History of Total Quality Management
In the early 1900s, Walter A. Shewhart introduced modern quality control and published a piece titled Economic Control of Quality of Manufactured Product in 1931 which set the stage for TQM. He was the first to make the connection between quality products and satisfied customers.
Later in 1954, Joseph M. Juran published a book called What Is Total Quality Control? The Japanese Way after he was invited to Japan to study their scientists and engineers.
He would go on to also publish Quality Planning and Analysis which further highlights how a holistic integration of certain principles and values can create improved organizational business processes that focus on continuous iteration to increase customer satisfaction.
W. Edwards Deming expanded on these ideas while also being in Japan post World War II by creating several TQM frameworks such as Deming's 14 Points, Deming's Seven Deadly Diseases of Management, and The Deming Wheel.
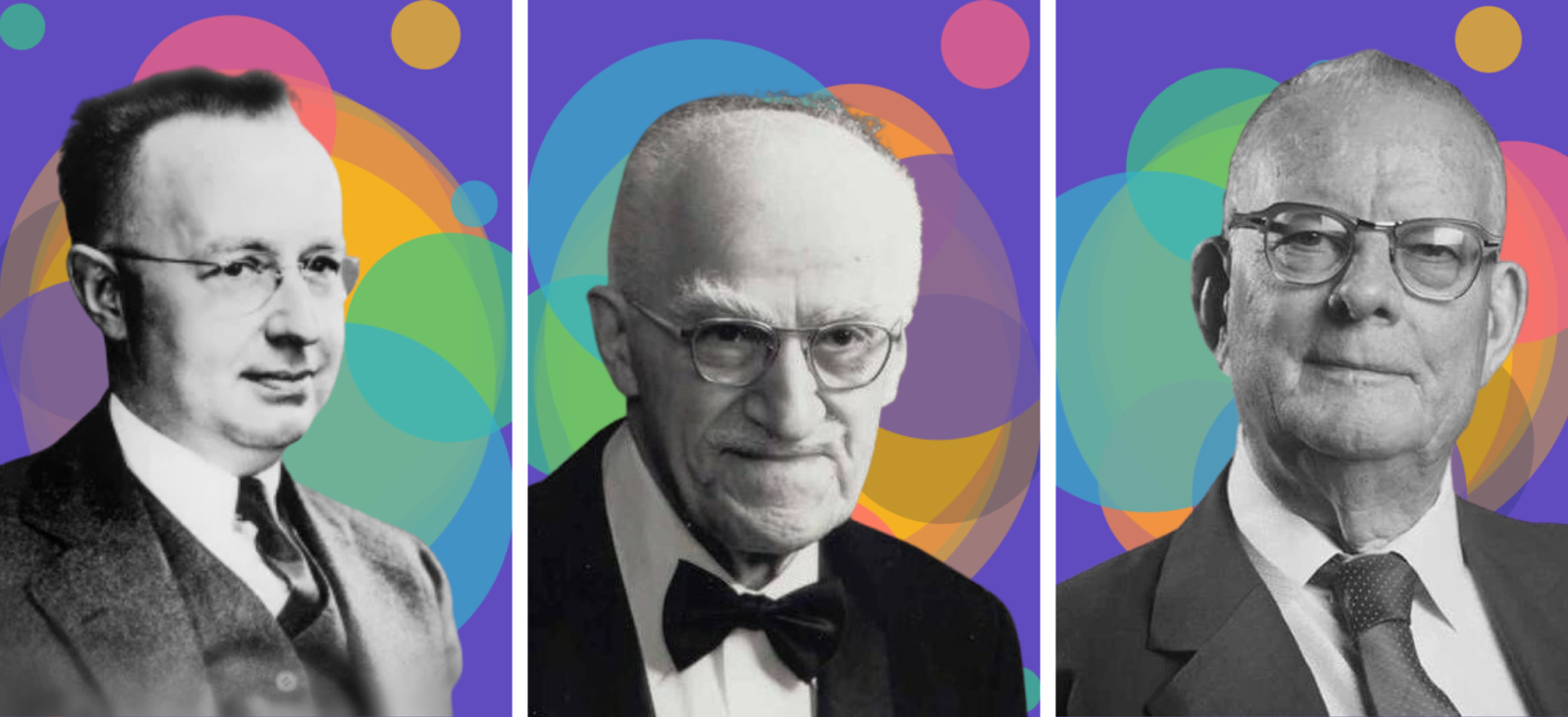
Nowadays we have to meet ever-evolving, yet strict quality assurance standards such as ISO 9000 and ESG 2015. As we move into the age of digital twins, artificial intelligence, and big data—how are the ideas of TQM expanding while holding true to their core principles? Let’s take a look.
The 8 Primary Principles of Total Quality Management
TQM is considered an ongoing customer-focused management approach that is about consistently improving business operations from all levels and in all aspects.
There are 8 universally accepted principles of TQM required to meet and exceed customer expectations:
- Focus on Customers: The overarching and top principle of TQM is that the customers define whether or not your products are high quality. An organization can work to improve all areas of the business but, in the end, the customer determines whether the efforts were worthwhile—which means post-market metrics to be consistently captured and analyzed.
- Full Employee Commitment: When an organization decides to adopt this management style, they must ensure all employees buy into the processes and system. This can only happen in an open workplace where employees don’t fear change and are empowered to learn while top management ensures the proper environment for success of TQM, including training.
- Strategic and Systematic Approach: The processes and procedures of each company should be a direct reflection of the organization's vision, mission, and long-term plan. This means quality and customer satisfaction are baked into the overall ethos of the organization and production process. All of which require a documented strategic plan for the long term.
- Adherence to Process: In TQM, it is believed that every activity can be deconstructed into a clear process that should be documented, adhered to, analyzed, and iterated on. Statistical process control is a cornerstone of TQM.
- Fact-based Decision Making: Being data-driven is at the center of TQM. Policies and procedures must be followed once implemented and then analyzed based on collecting data throughout the process flow to see opportunities for improvement.
- Effective Communication: During the adoption of TQM and throughout the day-to-day operations and initiatives, having clear communication channels that both employees and customers feel empowered to use is critical.
- Continual improvement: TQM is not a one-and-done thing. It requires an organizational mindset shift that requires continuous iteration for both process improvement and quality improvement.
- Integrated Systems: In TQM, systems should talk to each other, convey useful information across departments, and help make informed data-driven decisions. A shared vision, including knowledge of and commitment to the principles of TQM, keeps everyone on the same page.
In order to find success in total quality management, company-wide buy-in of every principle is critical. If a company can not achieve complete buy-in, the benefits of TQM can’t be realized.
This means working with all employees to make sure they feel like this is the best thing for them, the organization, and the customers.
Every person, team, and process throughout the organization is aimed at always delivering customer satisfaction to ensure long-term customer loyalty.
A common platform is imperative to achieve this buy-in. It’ll be easier to convince your team if they have a solution that provides full visibility into how their work will affect everyone from compliance all the way downstream to the customer.
If your quality management system isn’t connected to your other product management systems, it’s hard to get the full picture needed to be successful with total quality management.
The solution provider Propel, for instance, prides itself in working with customers and partners to help them realize true total quality management at their organizations and that's why Total Quality Management is already packaged together in their product value management (PVM) platform.
If you’re interested in being able to close the loop and connect the dots between all areas of your organization, see how Propel's modern QMS helps its customers bring TQM to life.
In Part II, we cover:
- The Pros and Cons of Total Quality Management
- Examples of Total Quality Management in Practice
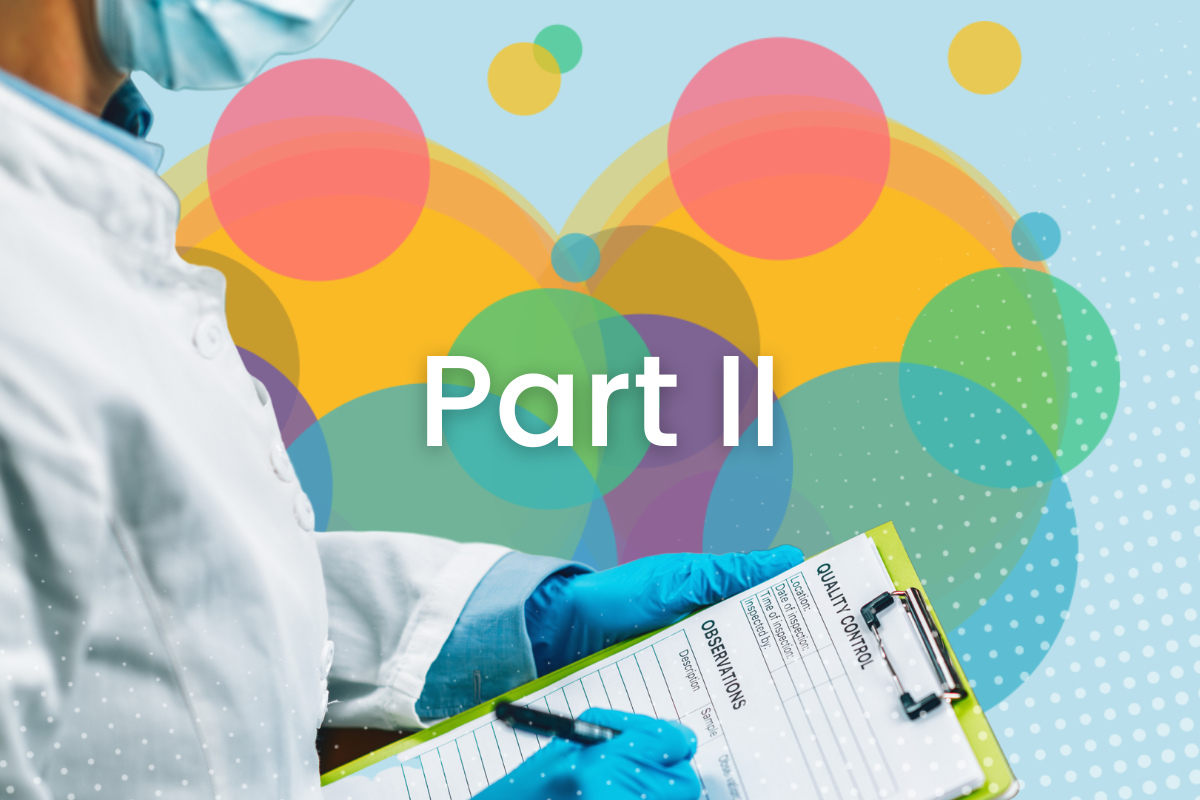
Click here to read PART II: The Pros and Cons of Total Quality Management
In Part III, we cover:
- How to Get Started with Total Quality Management in the Digital Age
- Tools of Total Quality Management
- How to Operationalize Total Quality Management at Scale
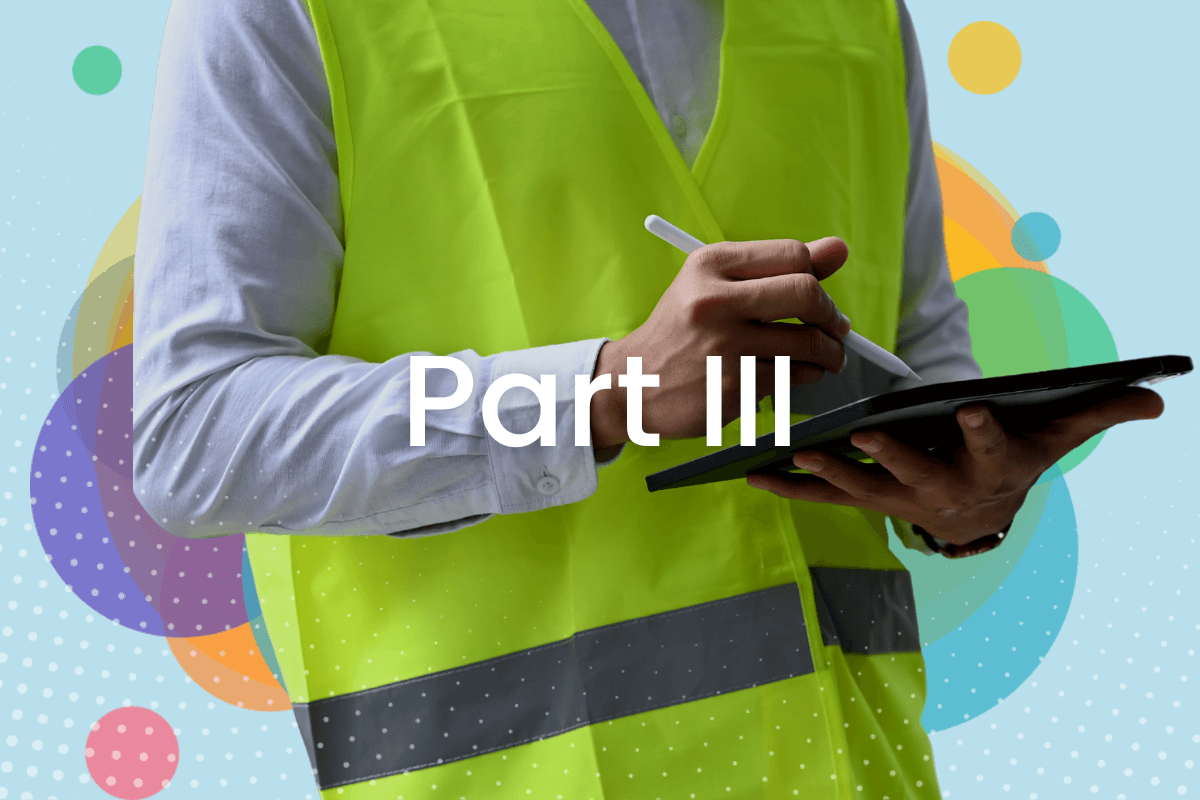
Click here to read PART III: How to Succeed with Total Quality Management in the Digital Age