Quality management functions as both a perspective and an approach to increasing customer satisfaction, cutting costs, and eliminating errors.
Quality initiatives start with product design and development and encompass the quality of incoming parts, through delivery and service. Quality should be built into a product, with a focus on solving problems as early as possible, whether in a regulated or non-regulated environment.
But it’s not easy. Challenges include lack of data control and access, slow and expensive response to quality and compliance issues, and difficulty identifying quality issues in the field.
When quality management is done well, you can mitigate risks, reduce costs and drive top-line growth, all while ensuring continuous improvement from concept to customer.
What is Quality Management?
Quality management is a comprehensive set of policies and processes that promote a series of cohesive improvement across the organization. It is the overseeing of all activities and tasks from product ideation to user adoption and customer support to ensure a high-standard of product excellence.
Quality management focuses on long-term goals through the utilization of short-term initiatives.
Harness the power of quality management with Propel's advanced Quality Management System (QMS). Propel QMS promotes higher product quality along every step of the value chain – explore it now.
Why is Quality Management Important?
A lot of different groups touch customers, such as marketing, sales, customer service, etc. Each one uses their own tech platform to do their jobs. When you have all these different groups using different platforms, the result is complexity, data latency and data loss.
For instance, something recorded by customer service on a field service platform has to be communicated by email or Slack to the quality team or the product team. And if these groups don’t communicate between themselves, the customer experience will be disjointed.
"The beauty of closing the loop with high-quality product management means that all these products are on the same platform, where data can be shared with a few clicks,” says Chuck Serrin, VP Industry Marketing, Medical Device & Life Sciences at Propel Software.
Quality management is important because it provides a framework for constant quality improvement. This acts as an assurance that companies never settle on delivering anything less than the best products and services possible.
This ties directly into carrying out quality policy - a statement detailing quality systems which align with an organization's purpose, mission, and strategic direction.
Quality is a very important attribute because it gives us a measurable way of differentiating between competitors in the marketplace. Consistency and reliability are two key factors to consider when it comes to product quality. With this in mind, quality management ends up creating a strategic source of value for companies across and even beyond the typical product lifecycle.
The 7 Principles of Quality Management
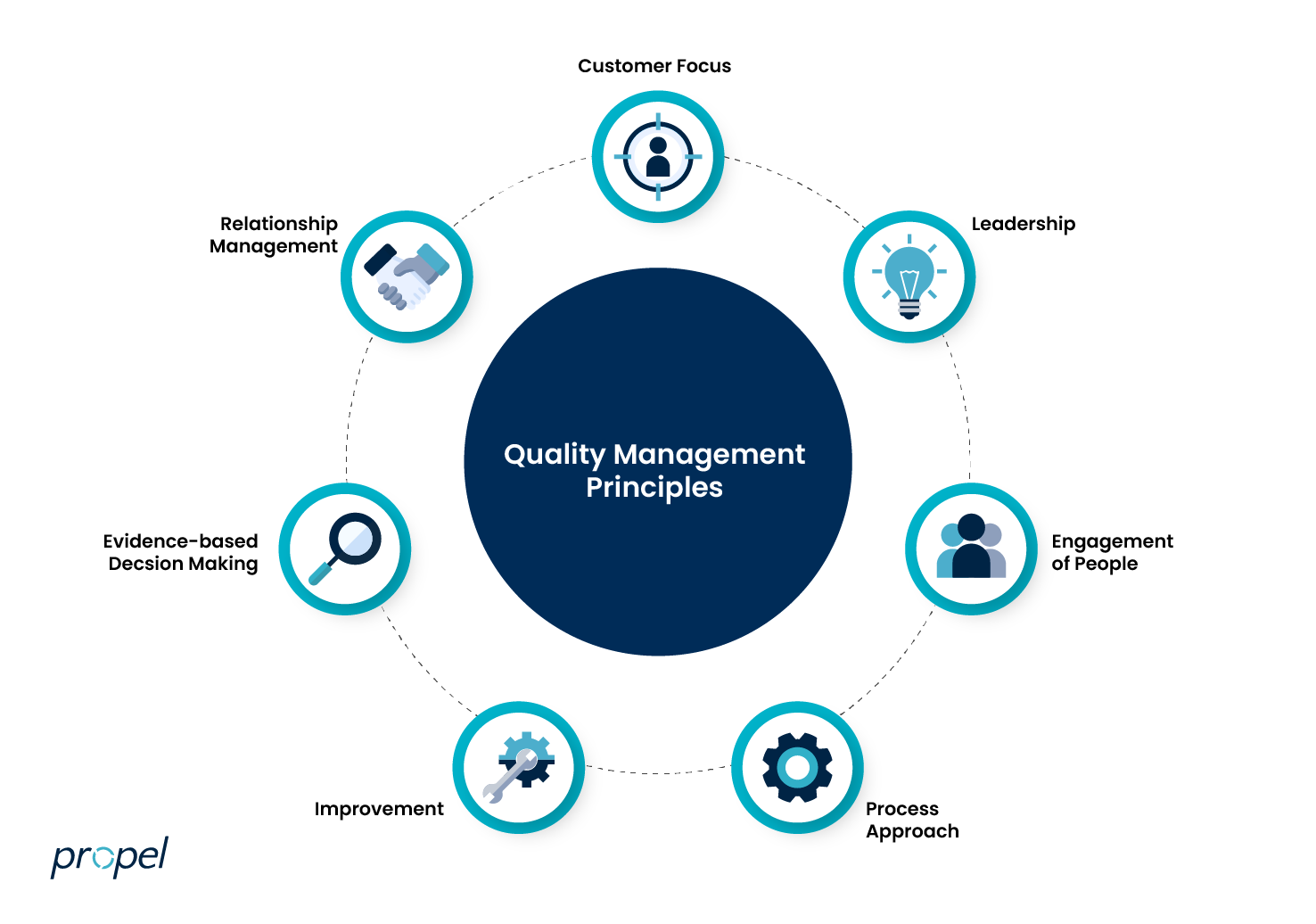
1. Customer focus
The primary goal of quality management is to meet external customer requirements and internal quality standards while striving to exceed customer expectations.
2. Leadership
The creation of conditions in which people are actively engaged in achieving organizational objectives through the establishment of unity across all levels.
3. Engagement of people
Nurture a work culture that ensures all people are competent, empowered, and engaged in delivering quality across all aspects of their work.
4. Process approach
Quality standards are achieved more effectively and efficiently when activities are understood and managed as interrelated processes that function as a coherent system working to complete a common goal.
5. Improvement
Focusing on consistent, small improvements is a proven pathway to success.
Risk management can also be helpful when considering how to improve, as it analyzes both internal and external factors to assess the health of a business and what the most appropriate action to take is.
6. Evidence-based decision making
Data is key to determining how successful quality management has been for your organization. Be sure to not only constantly collect data about your business processes, but also evaluate it and use what you discover to make decisions that produce the results you desire.
7. Relationship Management
In order to sustain the success of high quality products, organizations put effort into managing their relationships with external vendors all along the supply chain, such as shipping solutions providers. You should also build rapport and trust with your customers to build brand loyalty.
The Role of Quality Management
Quality management is tied directly to the performance and growth of a business.
"Eventually everything connects – people, ideas, objects. The quality of the connections is the key to quality, per se.” - Charles Eames
Avoid the common mistake of compartmentalizing quality. Total quality management (TQM) indicates the presence of interested parties in every department and at every level of an organization to ensure everyone is growing together.
The Four Stages of Quality Management
Quality management can be broken down into four distinct stages, according to the Six Sigma Plan-Do-Check-Act (PDCA) problem solving cycle.
1. Planning
Quality planning involves determining your goals and precisely how they can be achieved. At the same time, you should also identify who the key stakeholders are and what inputs and outputs are necessary to deliver quality products.
2. Developing
Manage your resources and engage in the activities necessary to achieve those goals. At the same time, continue to practice quality assurance as you work towards process improvement.
3. Evaluating
Check whether your goals have been achieved or not, using quantifiable performance metrics to determine whether key quality objectives have been met.
If they have, what could have gone better? If they haven’t yet, what went wrong?
This sort of statistical process control could involve monitoring process behavior, identifying areas of concern with internal systems, and finding solutions for any issues that occur during production.
4. Improving
Using what you have learned in the evaluation stage, improve the quality of future work by taking decisive corrective actions to improve organizational processes.
This is a cyclical, iterative process that should be consistently occurring at all levels of the organization.
What is ISO?
ISO, or the International Organization for Standardization, is a group made up of various business and industry leaders responsible for the development of quality management system (QMS) standards.
What is ISO 9001?
ISO 9001 is a specification of international standards for a quality management system. Think of this approach as a series of “how-tos'' for organizing processes and improving their efficiency, which in turn results in continual quality control across your entire organization.
Specifically, it denotes the following:
- Requirements for a QMS, including documented information, planning and determining process interactions
- Responsibilities of management
- Management of resources, including human resources and an organization’s work environment
- Product realization, including the steps from design to delivery
- Measurement, analysis, and improvement of the QMS through activities like internal audits, as well as preventive and corrective action
ISO 9001 standardization in particular also demonstrates that a company:
- Follows the guidelines of the ISO 9001 standard
- Fulfills any internal requirements
- Meets customer requirements as well as statutory and regulatory requirements
- Maintains up to date documentation for the above mentioned items
Following ISO standards has the byproduct of enhancing an organization’s credibility by showing consumers that its products and services not only have previously met, but continue to meet the needs of a rapidly changing market.
Examples of Quality Management
One of the most famous examples of quality management is Toyota. Toyota implemented a Kanban inventory control system, using a series of visual signals to improve efficiency on their assembly line. What this eventually created was a quality policy of maintaining a precise amount of both supply materials and inventory to fulfill customer orders as they were generated, allowing for the sustained growth of profit margins.
Another example of top-tier quality management is Coca-Cola. The beverage manufacturer ensures the best quality of their products through implementing globally accepted and authenticated manufacturing processes. The company closely measures their products, in addition to their packaging, to ensure their beverages meet the requirements of the company and expectations of customers. This results in continued innovation through the introduction of new products to the marketplace, which are a natural fit with their brand.
Why You Need a Quality Management System (QMS)
A quality management system is essential to any business’ success — and even more so in manufacturing. Propel Software provides the only quality management software that connects seamlessly with your CRM and PLM for a true closed loop that can quickly resolve your product issues, quality processes, and customer complaints in the field.